制造業(yè)轉(zhuǎn)移的趨勢走向與國家前途命運關(guān)系甚大。全球范圍內(nèi)出現(xiàn)過四次大規(guī)模的制造業(yè)遷移,而創(chuàng)新因素是推動制造業(yè)大遷移的重要動力。當前,制造業(yè)升級和遷移面臨的最大現(xiàn)實是全要素生產(chǎn)率的下降。
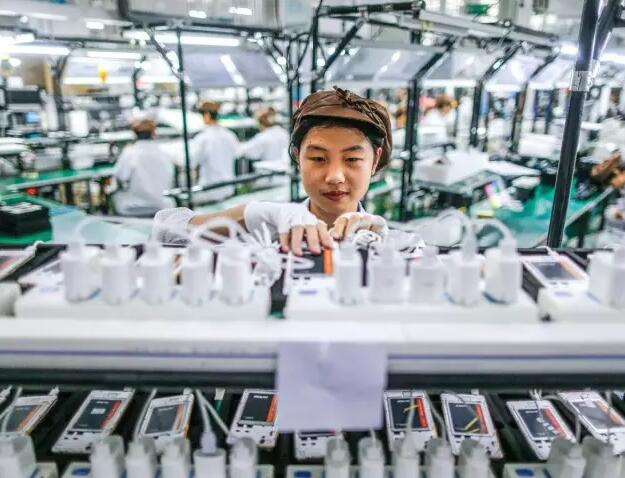
普遍認為,全球范圍內(nèi)出現(xiàn)過四次大規(guī)模的制造業(yè)遷移:第一次在20世紀初,英國將部分“過剩產(chǎn)能”向美國轉(zhuǎn)移;第二次在20世紀50年代年代,美國將鋼鐵、紡織等傳統(tǒng)產(chǎn)業(yè)向日本、德國這些戰(zhàn)敗國轉(zhuǎn)移;第三次在20世紀60至70年代,日本、德國向亞洲“四小龍”和部分拉美國家轉(zhuǎn)移輕工、紡織等勞動密集型加工產(chǎn)業(yè);第四次在20世紀80年代年代初,歐美日等發(fā)達國家和亞洲“四小龍”等新興工業(yè)化國家,把勞動密集型產(chǎn)業(yè)和低技術(shù)高消耗產(chǎn)業(yè)向發(fā)展中國家轉(zhuǎn)移,于是,30多年來中國逐漸成為第三次世界產(chǎn)業(yè)轉(zhuǎn)移的最大承接地和受益者。
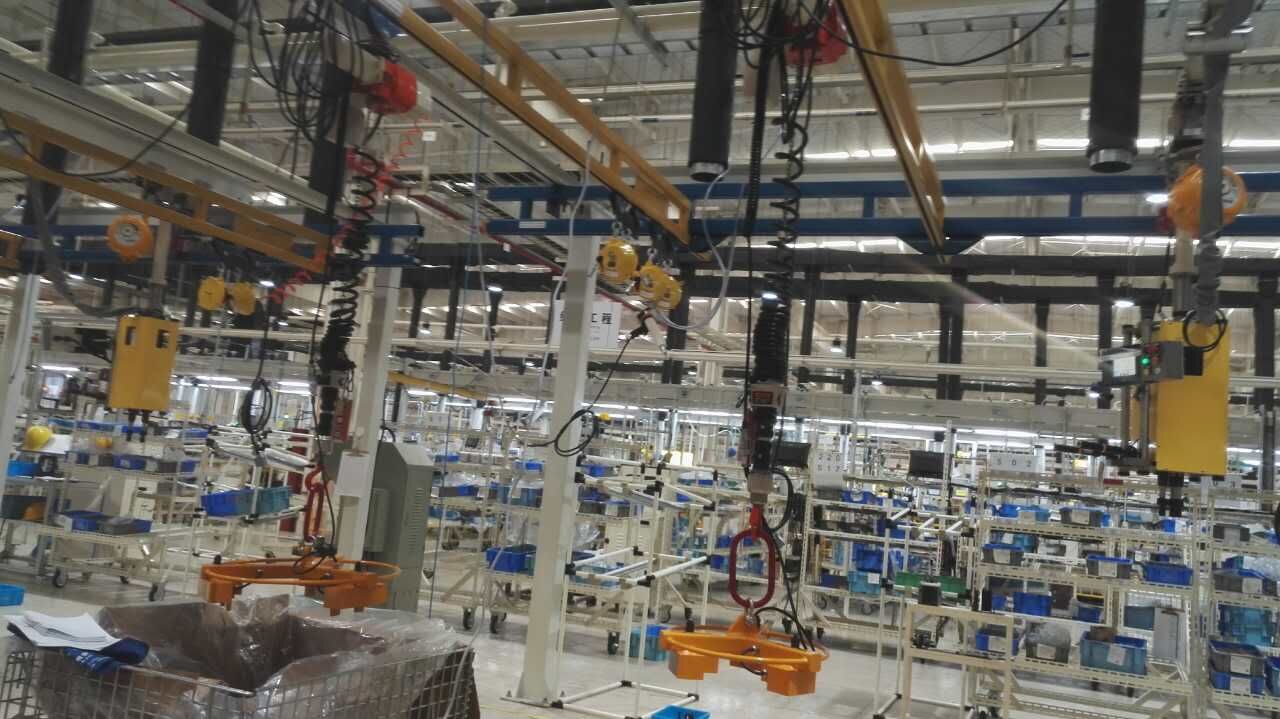
麥肯錫、波士頓咨詢集團等專業(yè)機構(gòu)以及各路經(jīng)濟學(xué)家和媒體,更多是從“成本結(jié)構(gòu)”(包括人力、土地、能源、制度性交易成本等綜合成本)的角度分析全球制造業(yè)轉(zhuǎn)移,進而研判未來制造業(yè)是否會流向印度、越南等低成本國家,或是由中國回流歐美。創(chuàng)新因素在全球制造業(yè)遷移過程中的重要推動作用,則并未獲得足夠關(guān)注。
美國:以制造流程創(chuàng)新承接全球,制造業(yè)轉(zhuǎn)移
美國承接全球產(chǎn)能轉(zhuǎn)移、實現(xiàn)制造業(yè)崛起的過程十分漫長,即使在1850年前后,美國已經(jīng)擁有世界上規(guī)模最大10家工業(yè)企業(yè)中的7家,也不表示美國真正成為制造業(yè)強國。在產(chǎn)業(yè)和技術(shù)競爭中,直到1920年前后,美國制造業(yè)才完全站上毫無爭議的世界之巔,這主要得益于美國在制造端、產(chǎn)品端上的全面創(chuàng)新。
20世紀初期的美國,四處閃動著偉大發(fā)明與偉大企業(yè),福特的T型車和凱迪拉克的電子啟動裝置開啟了人類的汽車時代,華納兄弟的《爵士樂歌手》帶動了有聲電影的繁榮,不銹鋼和人造樹膠重塑了美國制造業(yè),電話和電氣化使美國的工業(yè)基礎(chǔ)設(shè)施全面升級。
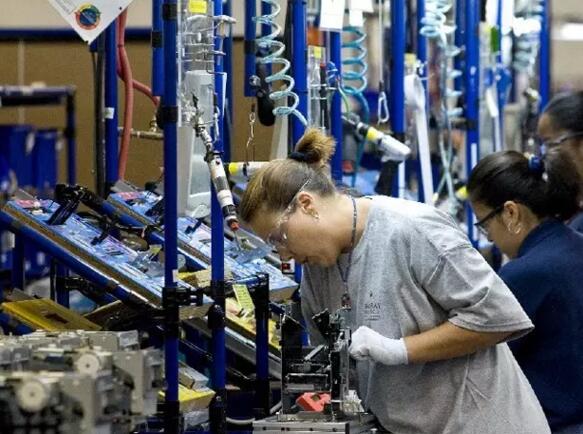
尤其是流水線生產(chǎn)方式的大范圍推廣,大規(guī)模批量生產(chǎn),除了能攤薄固定成本,也使大量工程師聚集在一起搞技術(shù)研發(fā),極大推動了科技創(chuàng)新。而當時英國工廠的組織形態(tài)相對傳統(tǒng),中小作坊是英國社會的最愛,但這類企業(yè)無法實現(xiàn)規(guī)模經(jīng)濟和成體系的研發(fā)創(chuàng)新。
到20世紀20年代年代,英國與美國在制造業(yè)領(lǐng)域的差距已十分巨大。當時有官方數(shù)據(jù)顯示,美國的研發(fā)支出在國民產(chǎn)值中所占比例高達2.5%,而同期的英國只有2%;美國土木工程師在總就業(yè)人口中所占比例已高達13%,大幅領(lǐng)先英國的5%。1929年,英國經(jīng)濟的三大支柱產(chǎn)業(yè)是鐵路船運、煙酒、紡織,而美國排名前三的優(yōu)勢產(chǎn)業(yè)是農(nóng)業(yè)設(shè)備與工程機械、車輛與航空器、鋼鐵和有色金屬。英國這樣一個志在全球角逐的工業(yè)大國,竟然沉淪到依靠煙酒生存。
日本、德國:以協(xié)作體系創(chuàng)新承接全球制造業(yè)轉(zhuǎn)移
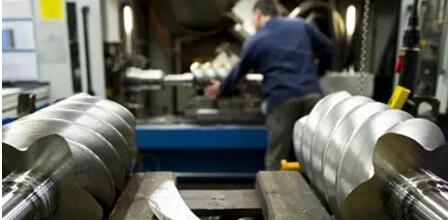
二戰(zhàn)結(jié)束以后,美國在執(zhí)行復(fù)興歐洲、日本的產(chǎn)業(yè)規(guī)劃中,讓德國和日本優(yōu)先發(fā)展鋼鐵、紡織輕工等傳統(tǒng)產(chǎn)業(yè)。但是,德日兩國不愿接受這個產(chǎn)業(yè)安排,如果被動接受低端制造業(yè)的轉(zhuǎn)移,在未來工業(yè)競爭中將永遠跑輸美國。此后,德國和日本不僅重點發(fā)展了汽車、機械、電子等高價值出口產(chǎn)業(yè),更重要的是,以高效完備的國家工業(yè)協(xié)作體系承接全球制造業(yè)轉(zhuǎn)移。
為什么德國和日本能夠擁有世界上最強大的中小企業(yè)群?德國將此稱為“隱形冠軍企業(yè)”,日本將此稱為“微小的世界頂尖企業(yè)”。德國和日本的產(chǎn)業(yè)結(jié)構(gòu)越來越精細化,很多公司幾十年只研究一種零件,只做一個產(chǎn)品,做到世界聞名,效益非常好。他們制造的產(chǎn)品,是基于自己看準的市場而磨煉出的獨有技術(shù),這些“隱形冠軍企業(yè)”不追求做大,而是力求成為具有某種世界第一的“唯一企業(yè)”。至今,中國很多高端制造業(yè)若不采用德國、日本的關(guān)鍵材料和核心零部件,比如航空玻璃、芯片、軸承、光電產(chǎn)品等,競爭力會大大下降。
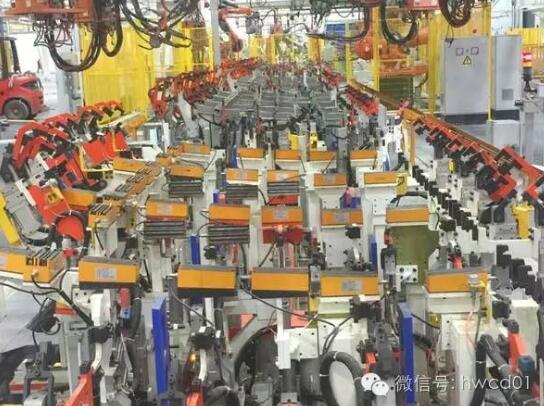
德國、日本的基礎(chǔ)工業(yè)技術(shù)世界領(lǐng)先,這是兩國在全球制造業(yè)大遷移中始終保持贏家地位的一大根基。舉兩個例子,中國稀土儲量是世界第一,但缺少技術(shù)把它變成材料。這些材料技術(shù)都是用幾十年的積累研究出來的,這些材料能做到納米級,擱在手機芯片里面。這些都需要專門的機床設(shè)備,這些東西美國也沒有,但德國和日本有。
半導(dǎo)體被稱為“信息化的糧食”,制造半導(dǎo)體芯片要使用高級光刻機,而全球70%的半導(dǎo)體光刻機由日本制造,德國供應(yīng)了其中最核心的光學(xué)元器件。光刻機是人類迄今所能制造的一切機械中最精密、最關(guān)鍵、最昂貴的設(shè)備,對晶片進行光刻操作時,定位精度達到0.01微米,相當于頭發(fā)絲的十萬分之一。
韓國:以產(chǎn)業(yè)鏈整合創(chuàng)新承接全球制造業(yè)轉(zhuǎn)移
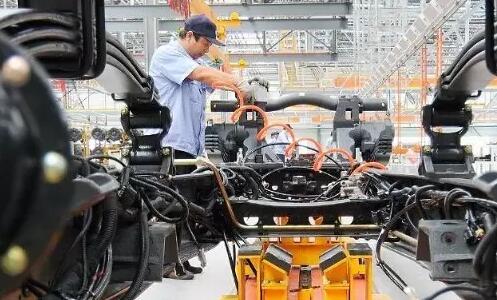
在制造業(yè)產(chǎn)能向亞太地區(qū)轉(zhuǎn)移的過程中,中國臺灣和韓國扮演了重要角色,其中,中國臺灣精于代工,韓國強于產(chǎn)業(yè)鏈整合,不過,不要忽視創(chuàng)新因素起到的作用。臺灣的半導(dǎo)體制造水平是世界級的,鴻海精密(大陸叫富士康)組裝了幾乎所有的蘋果iPhone、iPad,臺積電、聯(lián)發(fā)科則是芯片制造領(lǐng)域的世界級巨頭。
始于20世紀90年代初,由美國公司負責(zé)設(shè)計,中國臺灣負責(zé)代工做晶圓廠,投資巨大,從4英寸、6英寸、8英寸到現(xiàn)在12寸,從晶圓制造到切割、封裝、測試,都是臺灣不同的公司在做,形成一個前所未有的龐大產(chǎn)業(yè)鏈,占到全球芯片制造環(huán)節(jié)一半以上的市場份額。目前,臺積電已經(jīng)做到16納米工藝制程,大陸的華為海思、展訊一定要采用臺積電的工藝制程,才能使設(shè)計出來的高端手機芯片實現(xiàn)批量制造。
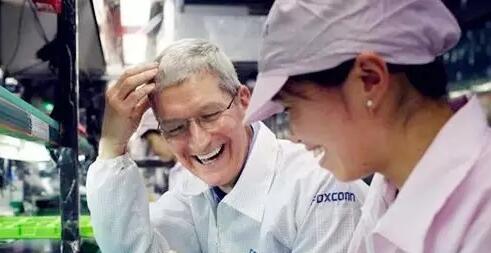
iPhone、iPad在蘋果公司也只是“實驗室產(chǎn)品”,能不能變成大眾消費品,中間有很大一道鴻溝——有沒有人能夠把這個產(chǎn)品大規(guī)模地生產(chǎn)出來。實驗室設(shè)計出一個產(chǎn)品,然后花很長時間制造出一件樣品,這不是太難的事。但是,大規(guī)模地制造,而且要那些沒有技術(shù)背景的工人去制造,這就需要規(guī)劃的流程非常合理,設(shè)計的模具非常精確。這里面涉及很多專利技術(shù),這些模具都是鴻海自己設(shè)計出來的,與蘋果公司是“交叉授權(quán)”的關(guān)系。也就是說,一款產(chǎn)品要實現(xiàn)量產(chǎn),就必須用到這些在生產(chǎn)工藝上的專利。
三星電子是韓國制造業(yè)的支柱,其國際競爭力是基于“全產(chǎn)業(yè)鏈”模式,即在芯片、閃存、液晶面板、平板電視、手機等全方位投資。三星“全產(chǎn)業(yè)鏈”模式追求的絕不只是成本優(yōu)勢,更重要的是技術(shù)積累和創(chuàng)新突破。
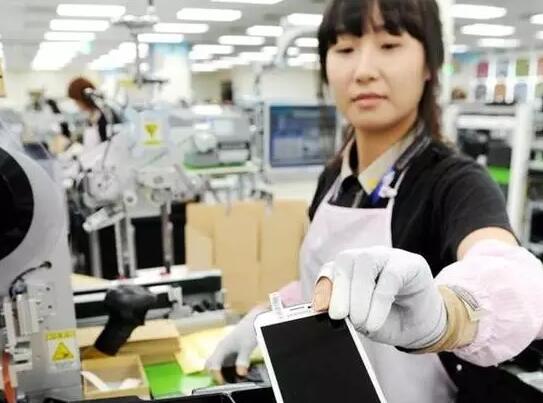
“全產(chǎn)業(yè)鏈”模式能使韓國三星深入了解技術(shù),實現(xiàn)高效的技術(shù)創(chuàng)新和產(chǎn)品創(chuàng)新。三星電子在成功掌握存儲、非存儲芯片技術(shù)后,又陸續(xù)掌握了TFT-LCD、PDP、有機發(fā)光顯示(OLED)、移動芯片、閃存芯片等核心技術(shù)。這些技術(shù)其實從根上說都是半導(dǎo)體技術(shù),這些半導(dǎo)體芯片技術(shù)很大程度上得益于前面對存儲芯片技術(shù)的深度掌握,再拓展到其他芯片技術(shù)就容易多了。
中國:以體系實力承接全球制造業(yè)轉(zhuǎn)移
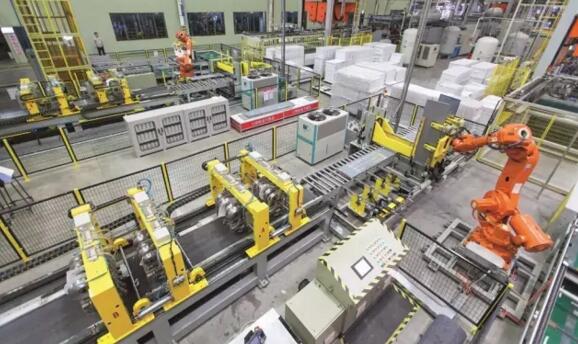
中國大陸真正開始承接全球制造業(yè)轉(zhuǎn)移,應(yīng)該是在2000年之后。目前,廣為人知的BAT(百度、騰訊、阿里巴巴),以及硬件制造相關(guān)的海爾、聯(lián)想、華為、中興、小米、富士康等廠商和品牌逐漸成熟,中國制造業(yè)已然形成一個自給自足、能為海外品牌代工也能推出自有產(chǎn)品的龐大體系。這個體系在2013年9月出版的英國《金融時報》中首度被統(tǒng)稱為“紅色供應(yīng)鏈”。目前,中國制造業(yè)的利潤率整體上仍比較低,但體系優(yōu)勢已經(jīng)形成。
中國出口的很多智能手機、家電和PC產(chǎn)品單品利潤率不到5%,人們想當然地認為,利潤的95%都被別人賺走了,企業(yè)家終日操心,工人累死累活,國家消耗資源、留下污染,最后只能從中賺點小錢。很多人并沒有搞清楚,這點利潤率的背后恰恰是中國強大的工業(yè)體系和市場體系。
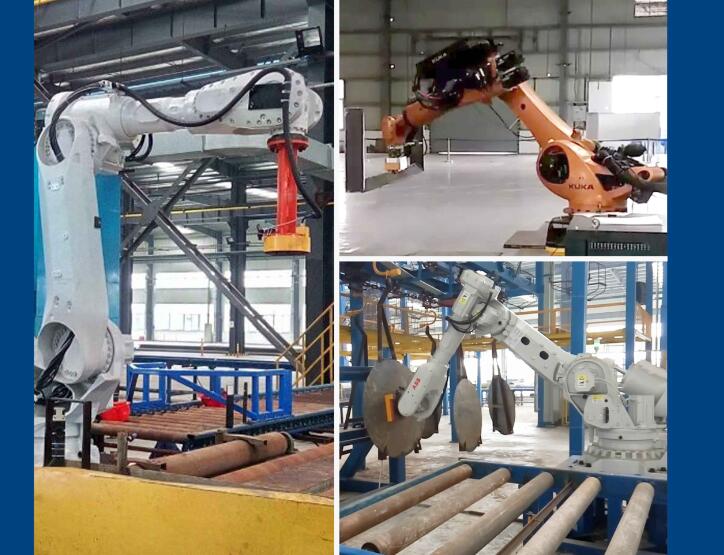
那95%的部分除了包括引進部分核心的、高端的電子元器件,更多是企業(yè)需要付給工人工資若干元,支付廠房租金若干元,支付水電費若干元,交納各項稅費若干元,付給代理商傭金若干元,支付物流費用若干元,付給配件商若干元……這才是構(gòu)成產(chǎn)品成本的最大部分。
之后,成本不會平白無故消失,只代表人民幣從一些人手中轉(zhuǎn)移到另一些人手中。配件商要供應(yīng)配件,毫無疑問又需要自己的人工、管理、廠租、水電、物流、倉儲等;供電局要供電,就需要電網(wǎng)建設(shè),電站建設(shè),乃至煤礦開采,電力裝備制造;物流公司要提供高效的物流,就需要車輛,需要司機,需要付費給高速公路;那么下一步,還需要筑路,需要鋼筋水泥,需要……表面上利潤率不到5%,骨子里則需要整個國家的原材料工業(yè)、能源工業(yè)、基礎(chǔ)設(shè)施、物流網(wǎng)絡(luò)、配套產(chǎn)業(yè)、市場體系的強力支持。
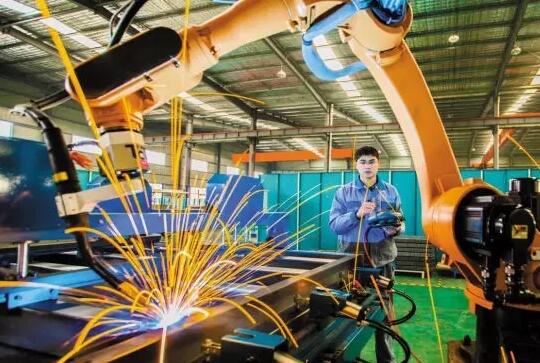
制造業(yè)的可靠和速度比價格更重要,缺貨絕對比高價帶來更多損失。依賴于中國對規(guī)模巨大且完整的供應(yīng)鏈和基礎(chǔ)設(shè)施的投資,中國供應(yīng)商在外國公司看來更加迅速,也更加可靠。
對于歐美日韓等制造業(yè)強國而言,“紅色供應(yīng)鏈”是一個亦友亦敵的體系。如果沒有它,諸如iPhone之類的許多新興產(chǎn)品可能無法在短時間上市,也不會是現(xiàn)在這個價格。但中國大陸透過這個體系所推出的自有產(chǎn)品,也挾著速度、彈性、低廉成本以及一些創(chuàng)意,讓傳統(tǒng)工業(yè)強國難以在某些市場與之競爭,因為他們?nèi)狈@個體系和條件。
創(chuàng)新驅(qū)動的最大障礙
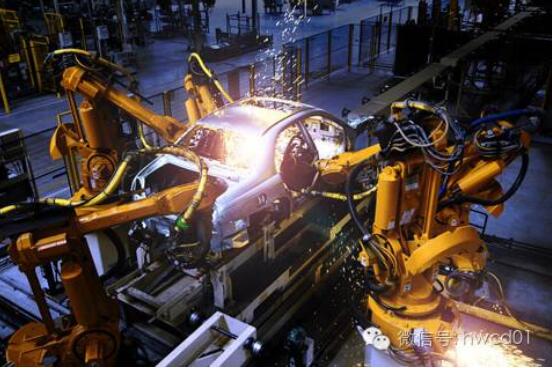
當今世界,制造業(yè)升級和遷移面臨的最大現(xiàn)實是“全要素生產(chǎn)率”的下降。媒體和經(jīng)濟學(xué)家更多關(guān)注國內(nèi)勞動條件的改變,例如“五險一金”制度實施、游資增加等緣故導(dǎo)致薪資和物價上漲等,以及市場和產(chǎn)業(yè)結(jié)構(gòu)的更替,致使中國大陸逐漸失去早期的成本優(yōu)勢。而“要素生產(chǎn)率”則更關(guān)注相對變化,比如2006年以來的這10年間,國內(nèi)勞動力成本上升了近5倍,這并不表示成本競爭力的必然削弱,如果自動化程度和組織效率提升更大的話。
過去,我們習(xí)慣性地將拉丁美洲、東歐和亞洲大部分地區(qū)看做低成本地區(qū),而將美國、西歐和日本看作高成本地區(qū)?,F(xiàn)今,這已是一種過時的世界觀了,工資、技術(shù)效率、能源成本、利率和匯率,以及其他因素年復(fù)一年的細微變化,悄悄地但也極大地影響了“全球制造業(yè)成本競爭力”圖譜。
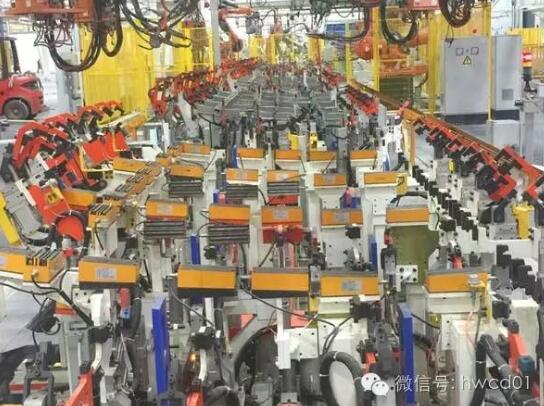
近十年來,全球的要素價格都不同程度出現(xiàn)上漲,但數(shù)字并不是其中關(guān)鍵,重要的是有沒有與業(yè)績掛鉤,與利潤相比,要素價格的上漲是否合理?遺憾的是,“全要素生產(chǎn)率”的下降已經(jīng)導(dǎo)致(甚至繼續(xù)導(dǎo)致)令人悲觀的制造業(yè)投資回報率。加上隔在科技創(chuàng)新與市場回報之間的玻璃墻,全球制造業(yè)將持續(xù)面臨悲觀前景。
現(xiàn)今,美國主流社會已不太關(guān)注來自中國的競爭,認為中國不可能憑新一代制造業(yè)取勝,而且逐漸形成關(guān)于“為何中國無法擁有下一代制造業(yè)”的完整論述。隨著智能機器人和3D打印等技術(shù)的日趨成熟,中國已無優(yōu)勢可言,跨國公司正想方設(shè)法將其高附加值的制造業(yè)遷回美國和歐洲。
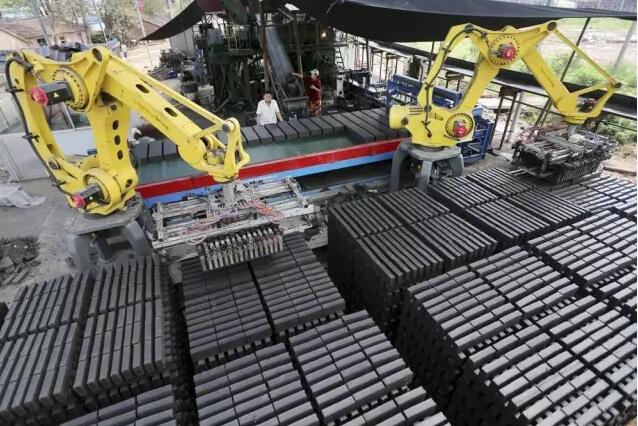
中國已經(jīng)啟動“中國制造2025”的十年計劃,旨在用先進的制造技術(shù),譬如機器人、3D打印和工業(yè)互聯(lián)網(wǎng)等,實現(xiàn)高效可靠的智能制造。同時,中國又啟動另一項國家計劃——“互聯(lián)網(wǎng)+”,尋求將移動互聯(lián)網(wǎng)、云計算、大數(shù)據(jù)和物聯(lián)網(wǎng)與現(xiàn)代制造業(yè)相結(jié)合。即使中國制造業(yè)在硬件上的轉(zhuǎn)型升級得以成功實現(xiàn),仍面臨三大現(xiàn)實挑戰(zhàn):
第一個挑戰(zhàn):歐洲、美國和中國的機器人耗費一樣的電量,同樣完全按指令工作,也不抱怨或加入工會。歐美工業(yè)企業(yè)有必要從世界各地運輸原材料和電子元件到中國,讓機器人完成成品組裝,然后再運回美國嗎?這完全沒有經(jīng)濟意義。歐美企業(yè)可以用差不多一樣的成本在本地進行生產(chǎn),去掉運輸環(huán)節(jié)。
第二個挑戰(zhàn):中國大多數(shù)機器人也不是在國內(nèi)生產(chǎn)的,即使有些是在國內(nèi)組裝的,仍然嚴重依賴從外國進口核心部件。
第三個挑戰(zhàn):歐美工業(yè)企業(yè)在中國招聘技術(shù)人才已經(jīng)有很大困難,因為先進制造業(yè)要求的管理和溝通技巧以及經(jīng)營基于復(fù)雜信息的工廠的能力。專業(yè)技術(shù)人才匱乏,已是中國推進先進制造業(yè)和服務(wù)業(yè)的軟肋。更何況,中國制造業(yè)已面臨主要對手超常規(guī)的競爭壓力。
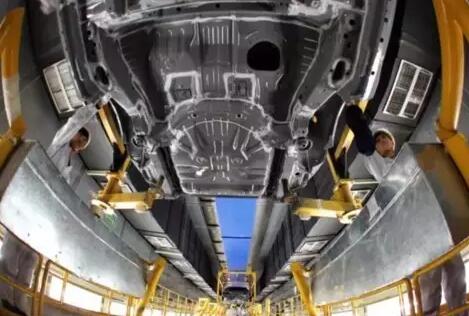
以制造業(yè)為支柱的中國經(jīng)濟,已經(jīng)到了最關(guān)鍵時刻,現(xiàn)在走的每一步都會對未來產(chǎn)生極其深刻的影響。
官方機構(gòu)在9月份權(quán)威發(fā)布的《中國制造2025藍皮書(2016)》指出,在智能制造技術(shù)應(yīng)用、制造業(yè)綜合成本變化等因素影響下,全球制造業(yè)布局逐漸調(diào)整:跨國公司制造業(yè)生產(chǎn)呈現(xiàn)向發(fā)達國家加速回流趨勢,同時,全球制造業(yè)正在加快向東南亞、南亞、非洲等成本更為低廉的地區(qū)轉(zhuǎn)移。前者是發(fā)達國家技術(shù)創(chuàng)新衍生的成本紅利,后者是低成本國家廉價勞動力優(yōu)勢正在產(chǎn)生吸引力。夾在兩者中間的中國制造業(yè),正在喪失勞動力成本優(yōu)勢,而技術(shù)和產(chǎn)業(yè)升級則面臨不小挑戰(zhàn)。
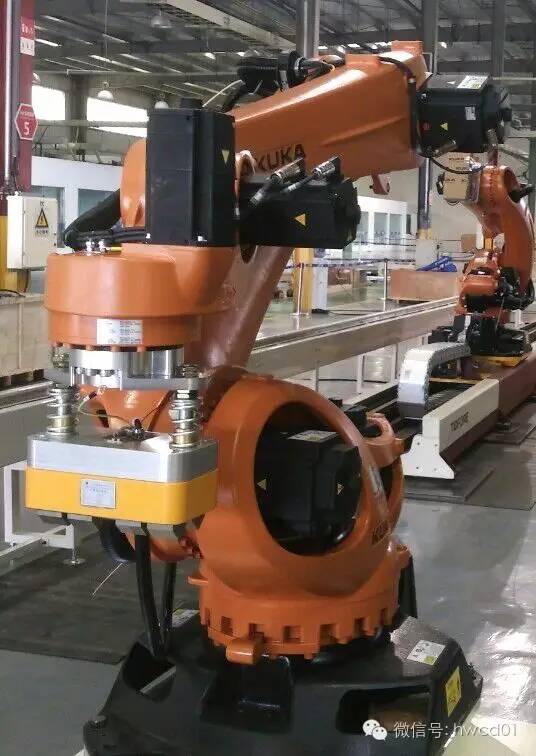
全球制造業(yè)大遷移趨勢
我國已在尋求降低中國企業(yè)綜合成本,即要素成本、交易成本和制度性成本,盡可能將更多制造業(yè)產(chǎn)能留在中國境內(nèi)。同時,國家創(chuàng)新體系正在加緊推進構(gòu)建當中,成本結(jié)構(gòu)的變化并不是問題核心,因為全球制造業(yè)大遷移背后的真正動力是技術(shù)創(chuàng)新和產(chǎn)業(yè)升級。
過去,傳統(tǒng)工業(yè)強國普遍傾向?qū)⒅圃飙h(huán)節(jié)外包給低成本地區(qū),這不是要退出制造業(yè),相反,恰恰是為了強化對產(chǎn)業(yè)鏈的控制。谷歌收購摩托羅拉,高調(diào)進入機器人領(lǐng)域并研發(fā)自動駕駛汽車,谷歌眼中的遠景規(guī)劃是,互聯(lián)網(wǎng)技術(shù)不斷融入制造業(yè)之后,可以建立起支配地位。一旦制造業(yè)各個環(huán)節(jié)都被“云計算”接管,將能夠?qū)χ圃鞓I(yè)產(chǎn)生足夠影響力甚至控制力。
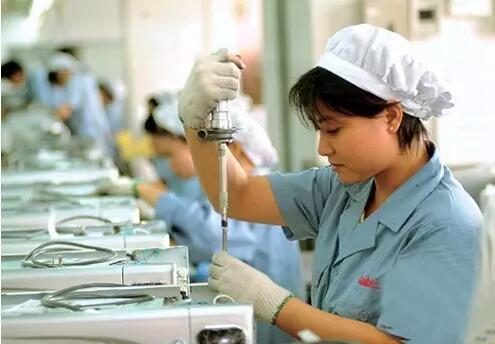
制造業(yè)轉(zhuǎn)移的趨勢走向與國家前途命運關(guān)系甚大,美國現(xiàn)在已退出很多制造領(lǐng)域,但是并未退出產(chǎn)業(yè)鏈,而是專攻標準和技術(shù)。日本目前也在按照這一路徑走,3D、4k、量子點等技術(shù)都是由日本開發(fā),并由中國企業(yè)發(fā)揚光大。如今,夏普、松下、東芝等轉(zhuǎn)型醫(yī)療設(shè)備、能源,特斯拉的電視就是松下在提供。
前沿技術(shù)和關(guān)鍵創(chuàng)新,依然是傳統(tǒng)工業(yè)強國的主戰(zhàn)場,中國制造商仍需跟蹤其技術(shù)路線。中國的“人口紅利”在消失,而“技術(shù)紅利”才剛剛開始。中國制造業(yè)整體上依然技術(shù)和資本積累不足,原始創(chuàng)新面臨高昂成本,而且風(fēng)險難測。
工業(yè)創(chuàng)新的真正拉動力是市場,中國制造業(yè)仍需要從小事、小創(chuàng)新開始做,很多小創(chuàng)新最后無意中可能會撬動大市場。中國制造業(yè)完全能依憑獨一無二的市場和供應(yīng)商體系,在全球制造業(yè)大遷移過程中創(chuàng)造優(yōu)勢,并掌握從制造材料到銷售通路的完整生態(tài)系統(tǒng)。
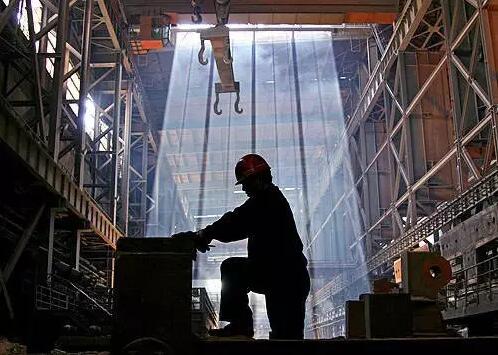
最近波士頓咨詢公司全球制造業(yè)成本競爭力指數(shù)顯示,世界經(jīng)濟體的制造業(yè)相對成本發(fā)生了變化,這促使很多企業(yè)重新思考過去幾十年對采購戰(zhàn)略的假設(shè)以及未來發(fā)展生產(chǎn)能力的地點選擇。在制定指數(shù)的過程中,智庫觀察到成本競爭力在多個經(jīng)濟體有所提高,而另一些經(jīng)濟體則相對下降。通過這個指數(shù),智庫發(fā)現(xiàn)制造業(yè)成本競爭力變化的四種顯著模式:
1.面臨壓力:過去一直被認為是低成本制造業(yè)基地的幾個經(jīng)濟體由于多項因素結(jié)合,自2004年來面臨著成本優(yōu)勢大幅減弱的壓力。例如:據(jù)估計,中國相對美國的工廠制造業(yè)成本優(yōu)勢已經(jīng)減弱到5%以下;巴西的制造業(yè)成本高于西歐;波蘭、捷克共和國和俄羅斯的成本競爭力也相對減弱,目前它們的制造業(yè)成本水平與美國相當,僅僅比英國和西班牙低幾個百分點。
2.繼續(xù)削弱:幾個過去十年制造業(yè)成本就相對高的經(jīng)濟體競爭力繼續(xù)削弱,它們的制造業(yè)成本高于美國16%-30%。主要原因是生產(chǎn)率的低增長和能源成本提高。競爭力繼續(xù)削弱的經(jīng)濟體包括:澳大利亞、比利時、法國、意大利、瑞典和瑞士。
3.保持穩(wěn)定:過去十年,很多經(jīng)濟體相對美國的制造業(yè)成本競爭力保持穩(wěn)定。在印度和印度尼西亞等經(jīng)濟體,雖然工資大幅增長,但生產(chǎn)率快速提高和貨幣貶值對成本起到抑制作用。相比印度和印度尼西亞的動態(tài)平衡,所有我們分析的成本驅(qū)動因素在荷蘭和英國都保持相對沒有太大變化。這四個經(jīng)濟體的成本競爭力使它們未來可能成為所在地區(qū)的制造業(yè)領(lǐng)先者。
4.全球新星:相比其他全球前25位出口經(jīng)濟體,墨西哥和美國的制造業(yè)成本結(jié)構(gòu)有更多的提升。由于工資增長率低、生產(chǎn)率持續(xù)提高、匯率穩(wěn)定和擁有巨大的能源成本優(yōu)勢,這兩個經(jīng)濟體現(xiàn)在成為全球制造業(yè)的新星。智庫估計,目前墨西哥按單位成本計算的平均制造成本低于中國。全球前10位商品出口國中,除了中國和韓國,其他經(jīng)濟體的制造業(yè)成本都高于美國。